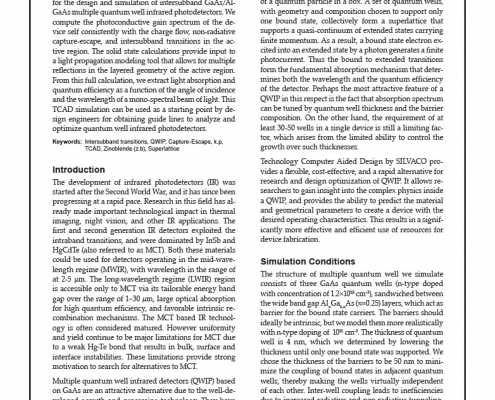
TCAD Simulation of Multiple Quantum Well Infrared Photodetector (QWIP)
We demonstrate the capabilities of SILVACO TCAD tools for the design and simulation of intersubband GaAs/AlGaAs multiple quantum well infrared photodetectors. We compute the photoconductive gain spectrum of the device self consistently with the charge flow, non-radiative capture-escape, and intersubband transitions in the active region. The solid state calculations provide input to a light propagation modeling tool that allows for multiple reflections in the layered geometry of the active region. From this full calculation, we extract light absorption and quantum efficiency as a function of the angle of incidence and the wavelength of a mono-spectral beam of light. This TCAD simulation can be used as a starting point by design engineers for obtaining guide lines to analyze and optimize quantum well infrared photodetectors.
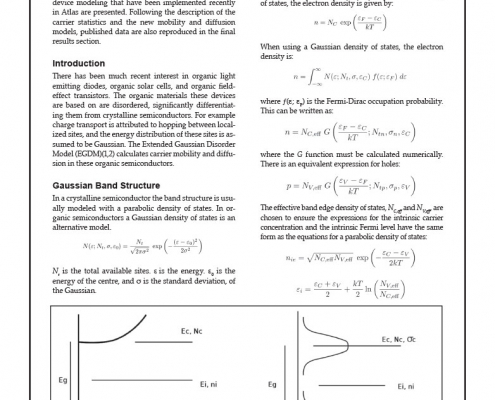
The Extended Gaussian Disorder Model in Atlas
In this article the various enhancements to the organic device modeling that have been implemented recently in Atlas are presented. Following the description of the carrier statistics and the new mobility and diffusion models, published data are also reproduced in the final results section.
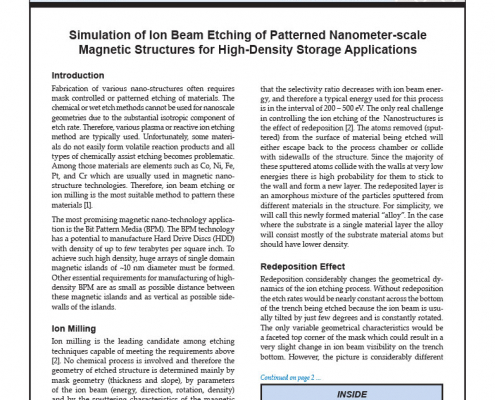
Simulation of Ion Beam Etching of Patterned Nanometer-scale Magnetic Structures for High-Density Storage Applications
Fabrication of various nano-structures often requires mask controlled or patterned etching of materials. The chemical or wet etch methods cannot be used for nanoscale geometries due to the substantial isotropic component of etch rate. Therefore, various plasma or reactive ion etching method are typically used. Unfortunately, some materials do not easily form volatile reaction products and all types of chemically assist etching becomes problematic. Among those materials are elements such as Co, Ni, Fe, Pt, and Cr which are usually used in magnetic nano-structure technologies. Therefore, ion beam etching or ion milling is the most suitable method to pattern these materials [1].
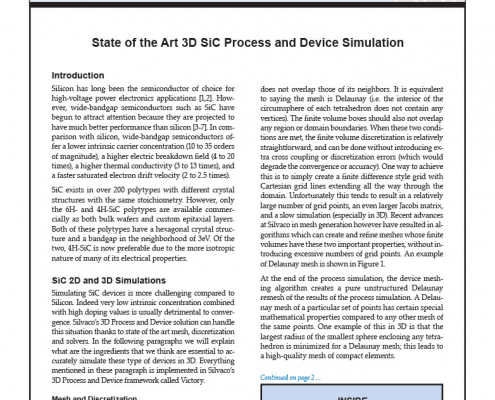
State of the Art 3D SiC Process and Device Simulation
Silicon has long been the semiconductor of choice for high-voltage power electronics applications [1,2]. However, wide-bandgap semiconductors such as SiC have begun to attract attention because they are projected to have much better performance than silicon [3-7]. In comparison with silicon, wide-bandgap semiconductors offer a lower intrinsic carrier concentration (10 to 35 orders of magnitude), a higher electric breakdown field (4 to 20 times), a higher thermal conductivity (3 to 13 times), and a faster saturated electron drift velocity (2 to 2.5 times).
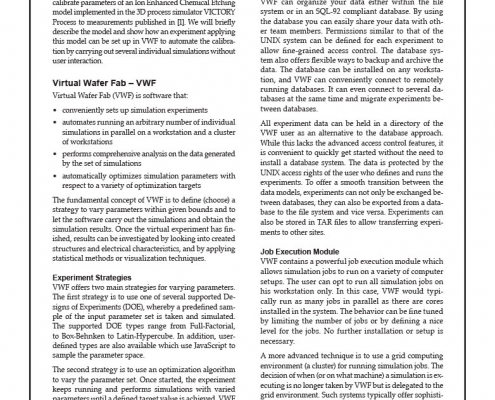
Calibration of the Ion Enhanced Chemical Etching Model of VICTORY Process Using Virtual Wafer Fab
In this article we describe a technique to automatically calibrate parameters of an Ion Enhanced Chemical Etching model implemented in the 3D process simulator VICTORY Process to measurements published in [1]. We will briefly describe the model and show how an experiment applying this model can be set up in VWF to automate the calibration by carrying out several individual simulations without user interaction.
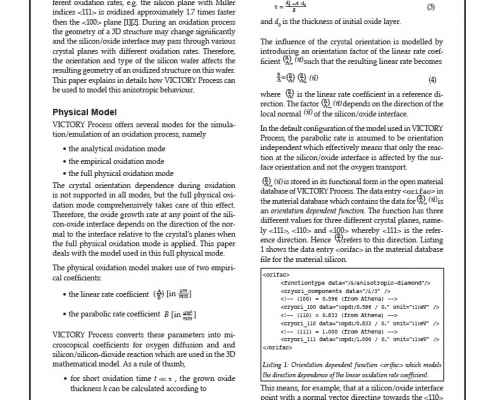
Using VICTORY Process to Model the Effect of Silicon Substrate Orientation on Oxidation Kinetics
Different crystal planes of silicon are known to have different oxidation rates, e.g. the silicon plane with Miller indices <111> is oxidized approximately 1.7 times faster then the <100> plane [1][2]. During an oxidation process the geometry of a 3D structure may change significantly and the silicon/oxide interface may pass through various crystal planes with different oxidation rates. Therefore, the orientation and type of the silicon wafer affects the resulting geometry of an oxidized structure on this wafer. This paper explains in details how VICTORY Process can be used to model this anisotropic behaviour.
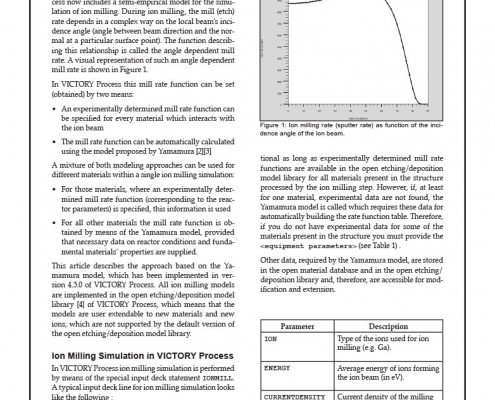
A Semi-Empirical Model for the Simulation of Ion Milling in VICTORY Process
The three-dimensional process simulator VICTORY Process now includes a semi-empirical model for the simulation of ion milling. During ion milling, the mill (etch) rate depends in a complex way on the local beam’s incidence angle (angle between beam direction and the normal at a particular surface point). The function describing this relationship is called the angle dependent mill rate. A visual representation of such an angle dependent mill rate is shown in Figure 1.
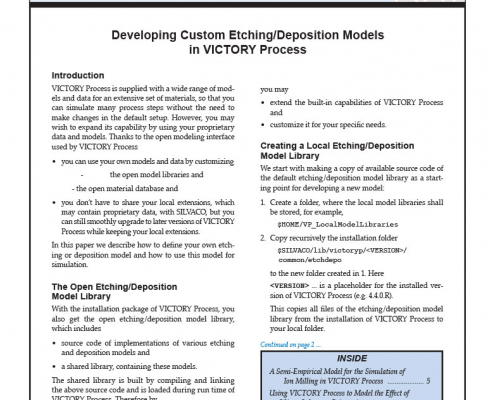
Developing Custom Etching/Deposition Models in VICTORY Process
VICTORY Process is supplied with a wide range of models and data for an extensive set of materials, so that you can simulate many process steps without the need to make changes in the default setup. However, you may wish to expand its capability by using your proprietary data and models. Thanks to the open modeling interface used by VICTORY Process
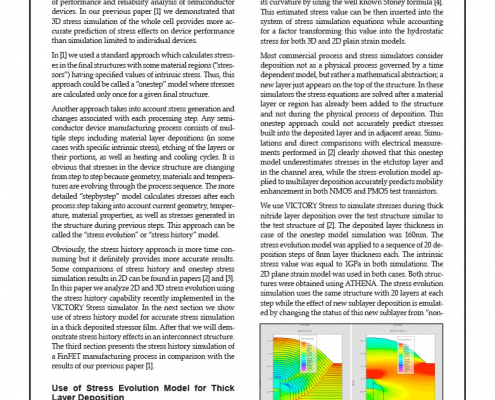
Simulation of Stress Evolution During Semiconductor Device Fabrication
Accurate stress simulation has become a necessary part of performance and reliability analysis of semiconductor devices. In our previous paper [1] we demonstrated that 3D stress simulation of the whole cell provides more accurate prediction of stress effects on device performance than simulation limited to individual devices.
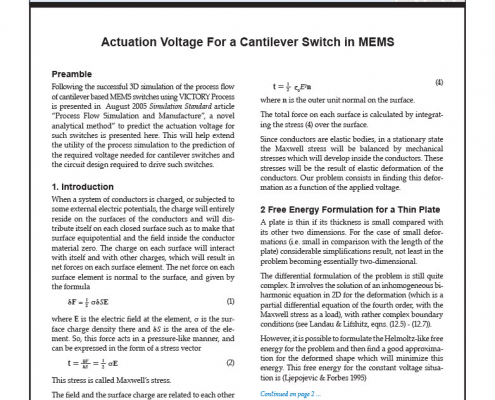
Actuation Voltage For a Cantilever Switch in MEMS
Following the successful 3D simulation of the process flow of cantilever based MEMS switches using VICTORY Process is presented in August 2005 Simulation Standard article “Process Flow Simulation and Manufacture”, a novel analytical method to predict the actuation voltage for such switches is presented here. This will help extend the utility of the process simulation to the prediction of the required voltage needed for cantilever switches and the circuit design required to drive such switches.